Carbon
-
Our vision:
To be recognised as a leading force in the delivery of a low carbon environment
-
Strategy:
Maximise energy and carbon efficiencies; deliver products with lower embodied carbon; support national and European carbon reduction targets
-
Action plan:
Achieve ISO 50001 certification and improve energy efficiency of production plants, increase the use of renewable energy specifically solar energy, and waste as fuel; reduce CO2 emissions from transport by extending our in-house fleet to gain greater control and optimise distribution.
-
2020 target:
Reduce carbon emissions by 10 per cent and energy emissions by five per cent per tonne of product based on 2010 baseline
Energy efficiency
Energy use per tonne rises
Overall energy use rose during the year, reflecting higher production levels, and energy use per tonne was also up. This was principally due to increased production of clay bricks, which is highly energy intensive, increased use of recycled asphalt planings (RAP) in our asphalt plants and a move in our concrete business to supply materials which are mixed at the plant rather than in the truck. This provides improved quality.
We continue to invest in new technology and to embed energy awareness by our support of Climate Week, quarterly conference calls on energy reduction and promotion of the message ‘switch it off’. In the second half of the year we decided to seek the ISO 50001 energy management standard as a means of complying with forthcoming ESOS legislation and to help drive energy improvements into the business. Work is under way on this programme.
Energy consumption

-
Energy consumption data
Energy consumption
2010 (baseline)
2012
2013
2014
Energy consumption – kilowatt hours per tonne
88,36 93.84 91.45 94.14 Energy consumption – total megawatt hours
3,625,045 3,456,777 3,769,717 4,070,549 Note: Historical data (kWh/tonne) adjusted to reflect updated production figures
Target: 5 per cent reduction based on 2010
Waste as fuel
Waste fuel use increases
We continue to invest in new facilities at our three cement works to enable greater use of alternative fuels. These include profuel – a solid kiln fuel manufactured from paper, plastic and fibrous wastes that are either uneconomic or impossible to recycle – and solid recovered fuel (SRF), which is made from domestic waste and biomass. Overall use of waste as a fuel in our cement kilns continues to rise and the use of biomass also increased to 16%.
-
Cement fuel derived from waste - tonnes data
Cement fuel derived from waste
2010 (baseline)
2012
2013
2014
All waste
158,704 (53%)
140,096 (54%)
181,738 (58%)
207,121 (61%)
Biomass
72,727 (23%)
57,081 (16%)
57,128 (13%)
75,837 (16%)
Target: 35 per cent use of biofuel by 2020
CO2 emissions from production
Carbon conversion factor affects results
There was an 11 per cent rise in kilogrammes of CO2 per tonne of production due to a different mix of energy generation and a change in the carbon conversion factor applied to energy use, principally electricity. Our renewable energy programme is continuing and we are looking particularly at sites with potential for solar generators.
CO2 emissions from production
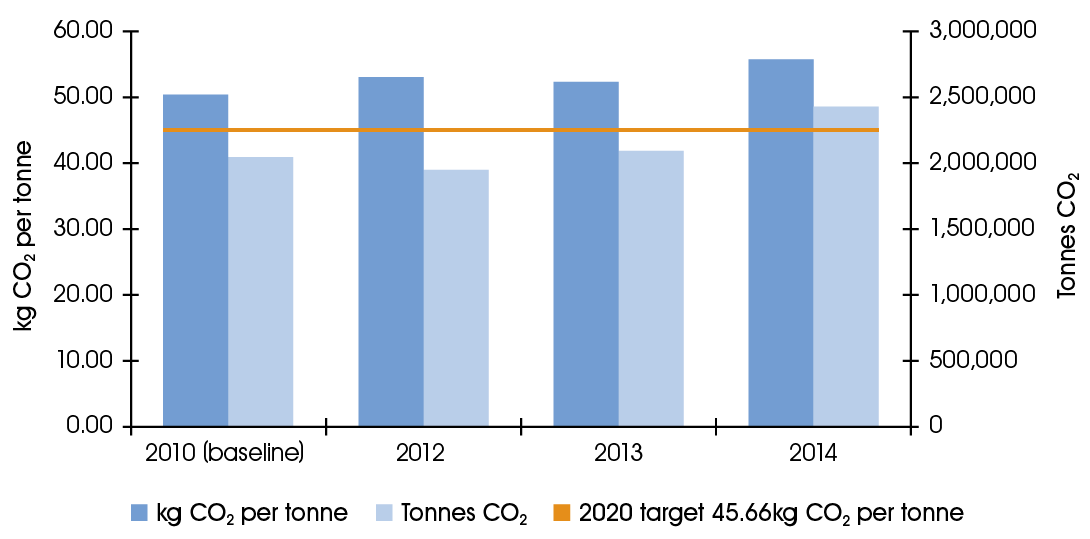
-
CO2 emissions from production data
CO2 emissions from production
2010 (baseline)
2012
2013
2014
Kilogrammes of CO2 per tonne of product
50.73
53.62
52.87
56.68
Tonnes of CO2 from production
2,081,310
1,975,206
2,179,521
2,450,699
Note: Historical data (kg CO2/tonne) adjusted to reflect updated production figures.
Target: 10 per cent reduction in carbon emissions by 2020 based on 2010 baseline
CO2 emissions from transport
Improvements in vehicle scheduling
CO2 emissions from transport on a per tonne basis fell slightly during the year partly as a result of similar reduction in distance carried per tonne. This is an impact of opening sites again after closures in previous years. The average CO2 emissions for the 161 fleet cars we purchased for employee use in 2014 was 124g/km compared to a fleet market average of 137g/km and a total market average of 140g/km.
A project to centralise, standardise and optimise order handling and vehicle scheduling in the aggregates, asphalt and concrete business lines is ongoing. The aim is to improve vehicle use and reduce fuel costs. The project is focused on the effective and efficient use of our delivery fleet through the introduction of vehicle optimisation software and a material resource planner (MRP) to schedule internal deliveries. All aspects of distribution are now managed by the logistics team reporting to a UK supply chain director.
Transport efficiency
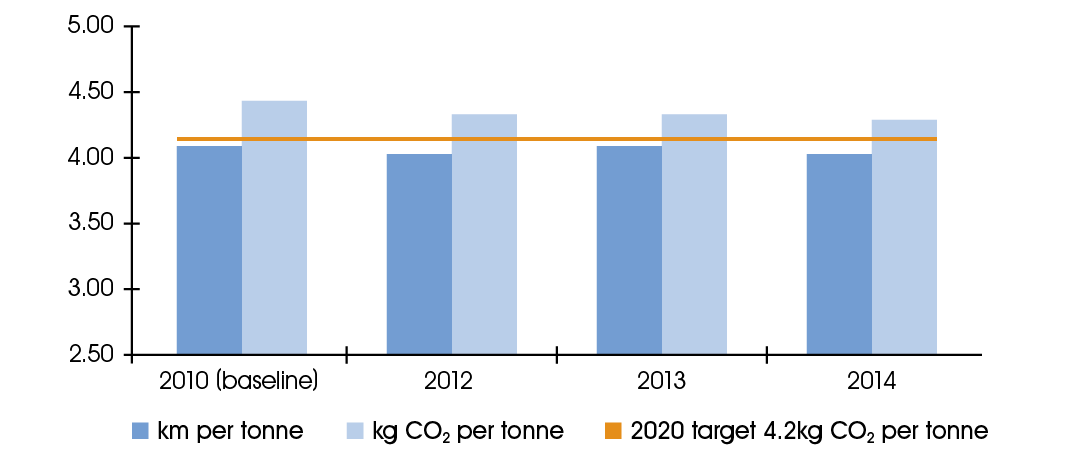
-
Transport efficiency data
Transport efficiency
2010 (baseline)
2012
2013
2014
Tonnes delivered
31,503,169
26,570,201
28,626,905
29,952,430
kg CO2 / tonne
4.42
4.36
4.37
4.31
Total distance travelled km
129,408,218
107,504,846
117,251,403
121,162,796
Tonnes CO2 / year
139,380
115,956
125,236
129,171
Note: 2013 data amended to correct an error in previous data
Target: Reduce CO2 emissions by five per cent per tonne by 2020 based on 2010
Mode of transport %
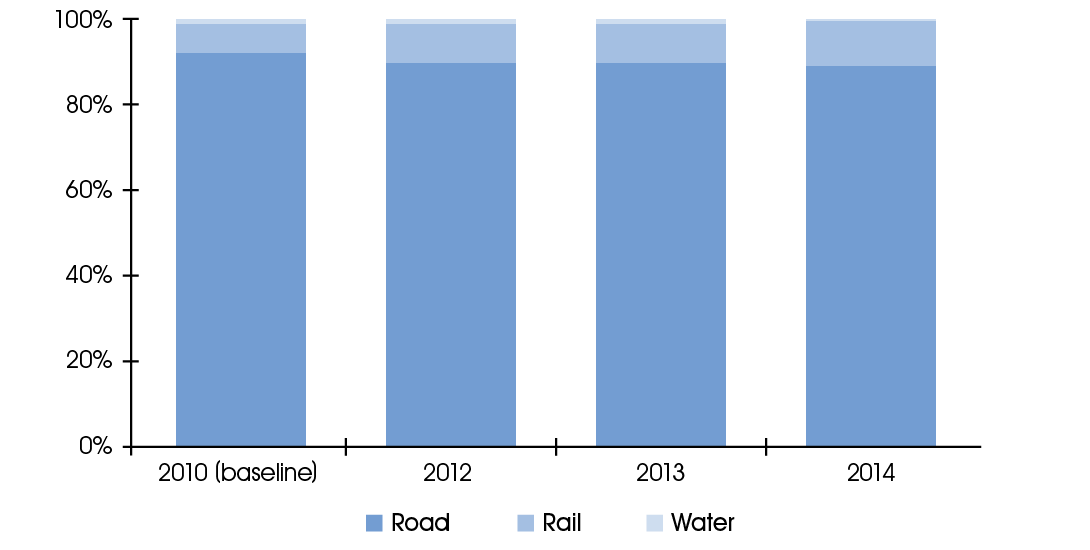
-
Mode of transport data
Mode of transport
2010 (baseline)
2012
2013
2014
Road
91.36
89.50
89.55
88.9 Rail
7.42
9.19
9.23
10.7 Water
1.23
1.31
1.23
0.5
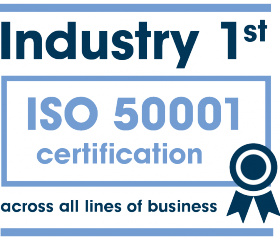
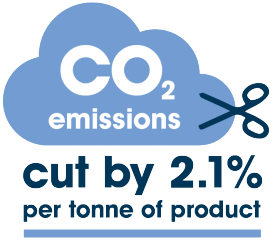
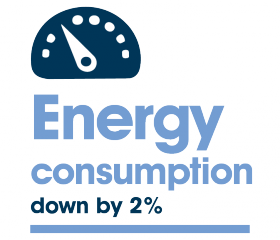
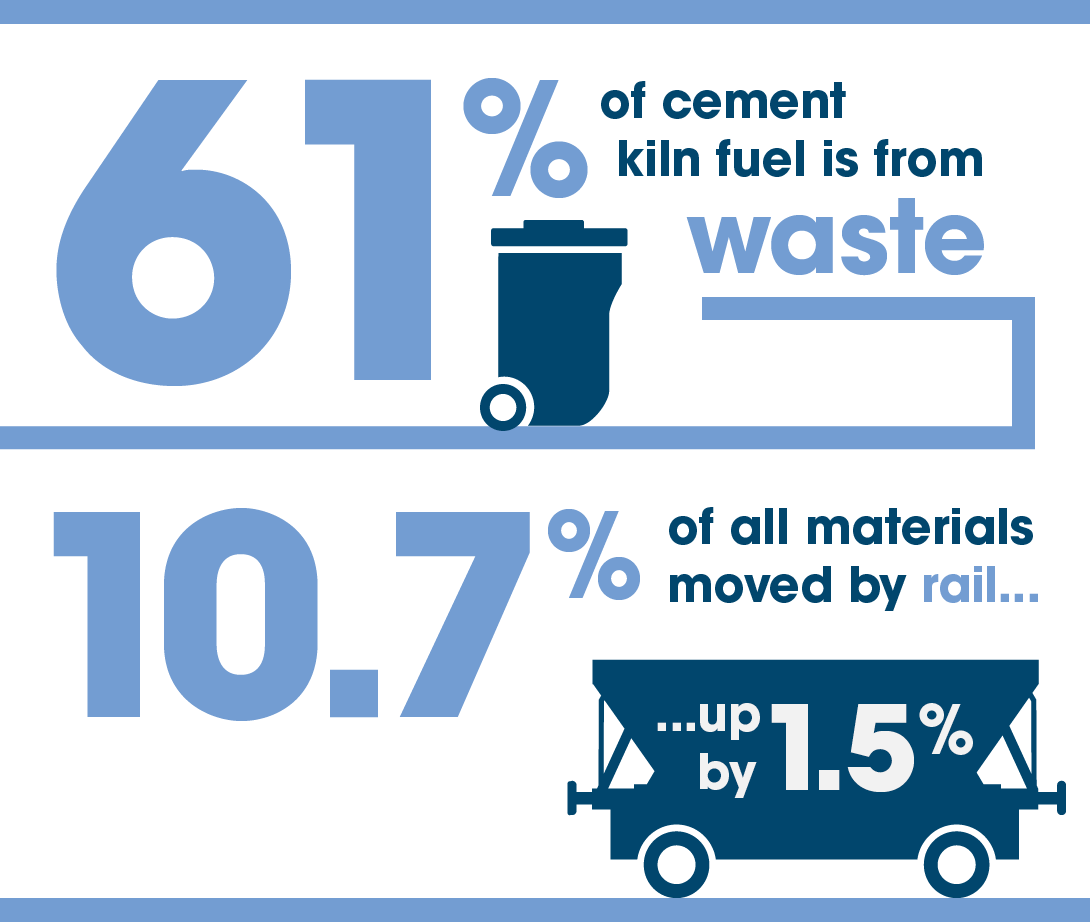
Mill fan upgrade cuts energy use
A fan upgrade at the Purfleet Regen works in Essex has resulted in a 50 per cent reduction in energy on one of the grinding mills, reducing CO2 emissions by 1,487 tonnes per year. Read more
Ketton solar plant wins industry award
The eight megawatt solar energy site at Ketton cement works in Rutland has won a top industry award. Read more
Five-star rating for cement fleet
Hanson Cement has joined the ECO Stars fleet recognition scheme and been given a five-star rating. Read more