Waste and raw materials
-
Our vision:
To be recognised as a responsible business which uses both raw materials and waste beneficially and has a minimal impact on the environment.
-
Strategy:
Conserve natural resources by avoiding or reusing waste; develop products that have low embodied impacts;
-
Action plan:
Minimise waste and improve material efficiency and recycling as defined in the waste heirarchy; maximise production efficiency; deliver the Right first time campaign to improve product quality and customer service.
-
2020 targets:
Reduce non-process waste to landfill by 85 per cent; increase use of recycled materials in products.
Waste minimisation
Waste to landfill down by a further 29 per cent
We reduced waste to landfill by a further 29 per cent during the year with the biggest fall coming in asphalt where we recycled a lot more filler dust into the product. Some filler dust was stock-piled, but the general trend remained positive. We have now achieved a 62 per cent reduction based on 2010.
The majority of our sites are included within a single contract with Biffa a national waste disposal company which enables us to control the process more effectively and provide further data on the quality and types of waste being produced. Dry mixed waste bins have been provided at all our sites to collect recyclables including plastic, paper and cardboard. The waste is taken to a network of depots for recycling with any residue used for energy recovery.
Waste to landfill
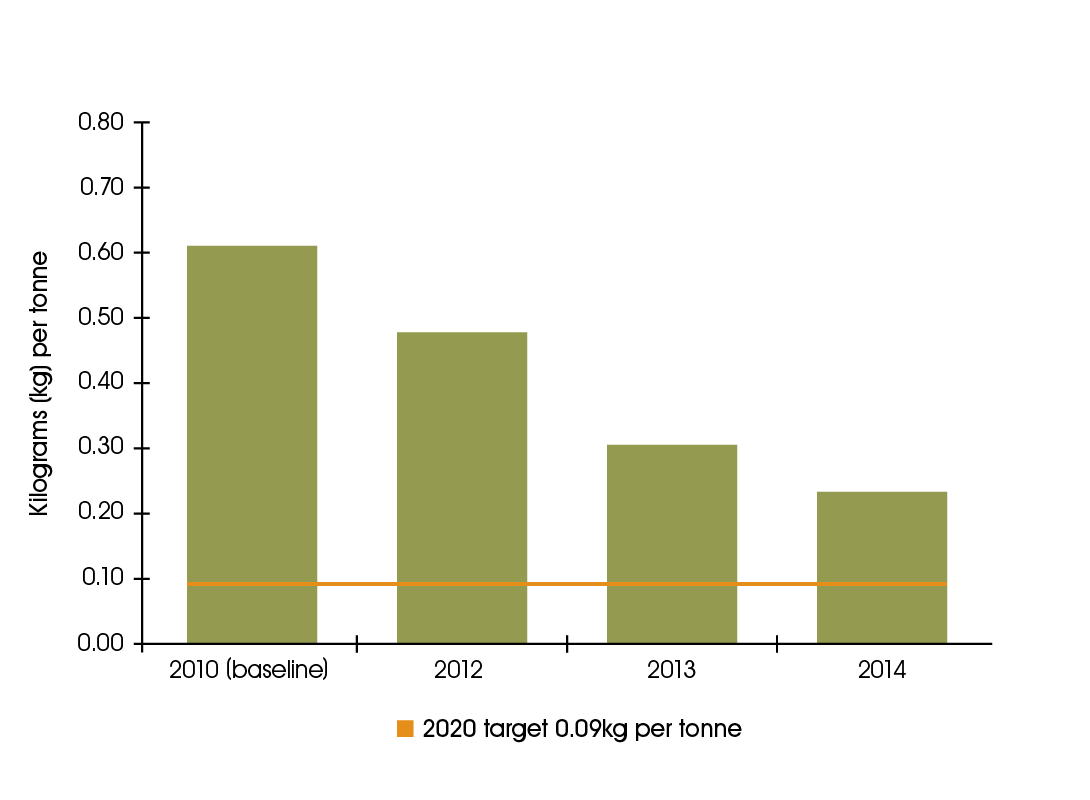
-
Waste minimisation data
Waste to landfill
2010 (baseline)
2012
2013
2014
Total tonnes
21,950
16,693
12,401
9,573
Kg/tonne product
0.61
0.48
0.33
0.23
Target: Reduce total waste to landfill by 85 per cent by 2020 based on 2010 baseline
Click here for data by business line
Cement specific waste – by-pass dust – tonnes
2010 (baseline)
2012
2013
2014
Produced
5,619
11,597
5,782
9,335
Landfilled
2,979
0
0
0
Diverted from landfill
47%
100%
100%
100%
Materials efficiency and recycling
Regen boosts cement replacement
The cement replacement Regen (ground granulated blastfurnace slag) reduces embodied CO2 in concrete and provides a number of other benefits. Its use in ready-mixed concrete means we have one of the highest cement replacement rates in the UK market. We are working towards our target of 45 per cent cement replacement by 2020 and are developing mixes with higher Regen content as well as developing improved communication of the CO2 benefits of these products to customers.
Over half of our asphalt plants can use recycled asphalt planings (RAP) in base course mixes at rates of up to 25 per cent. The national average is around nine per cent (including the use of filler dust, a by-product). Our target for 2020 is 10 per cent, excluding filler dust and in 2014 we improved from 4.54 to 5.63 per cent. Midland Quarry Products has a particularly good track record in the use of RAP and we are introducing techniques developed at MQP into other parts of the business.
Concrete sites recovering surplus
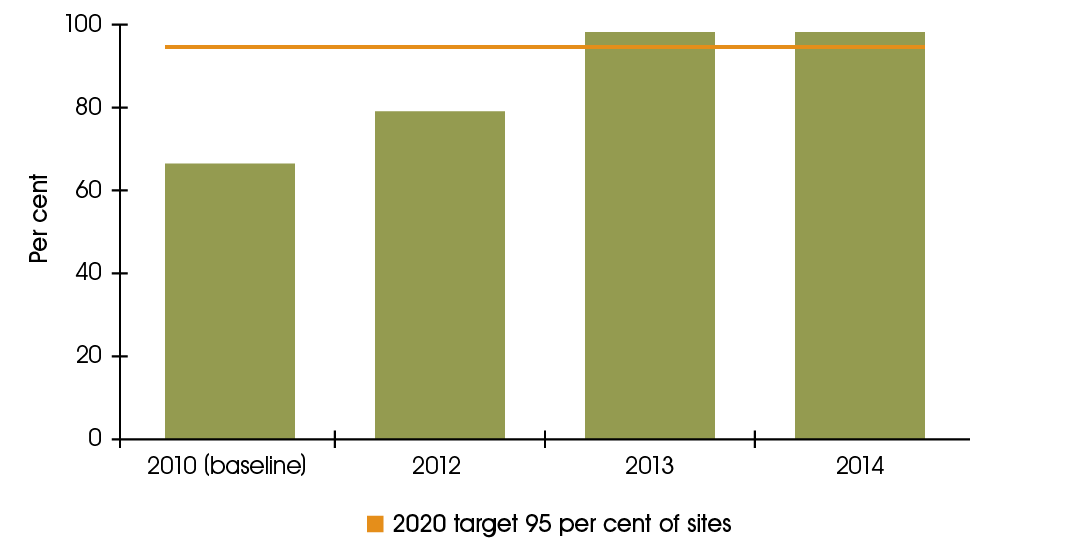
-
Recycled and secondary materials data
Recycled and secondary materials data
2010 (baseline)
2012
2013
2014
Definition
By-products or waste used as raw material in cement
5.31 6.21
6.43
7.52
Regen and any alternative material as a % of total cement and Regen production
Recycled aggregates used in precast concrete and concrete blocks
55.51 50.73
62.08
55.49
Recycled aggregate as a % of total aggregates used
Cement replacements used in precast concrete and concrete blocks
11.19 9.48
9.21
4.87
Cement substitutes as a % of total cement use
Clay replacements in bricks
1.99 4.48
4.98
7.05
Recycled materials used as a clay replacement
Aggregates recycled and sold
1.63 1.38
1.31
1.43
Sales
Recycled aggregates in asphalt
2.88 2.60
4.54
5.63
% of recycled aggregate used in asphalt
Recycled aggregates in concrete
0.08 0.20
0.62
0.18
% of recycled aggregate used in ready-mixed concrete
Sites which recover surplus concrete
65 79
99
99
Sites recovering over 50% of process waste (inc third party recycling)
Cement replacements in concrete (Regen, PFA)
38.43 39.92
37.47
37.19
% of cement substitutes in ready-mixed concrete
Targets: Increase cement replacements in concrete to 45 per cent; recycled aggregate in asphalt (excluding filler dust) to 10 per cent and concrete plants recycling surplus concrete to 95 per cent - all by 2020.
Product quality and performance
Product quality is critical
Product quality and customer service are critical to our business and we are devoting an increasing amount of resources to these areas to improve performance.
Our aim is to grow a loyal customer base, generate repeat business, and eliminate complaints by delivering the highest levels of product quality and service. We have made improvements within our customer service centres to ensure our customers receive the right products at the right time and are invoiced correctly. We continue to invest in development of new products, either working with external partners or the HeidelbergCement Technology Centre in Germany.
Target: Reduce production waste by getting it right first time
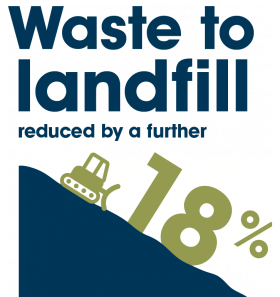
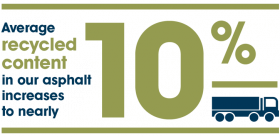
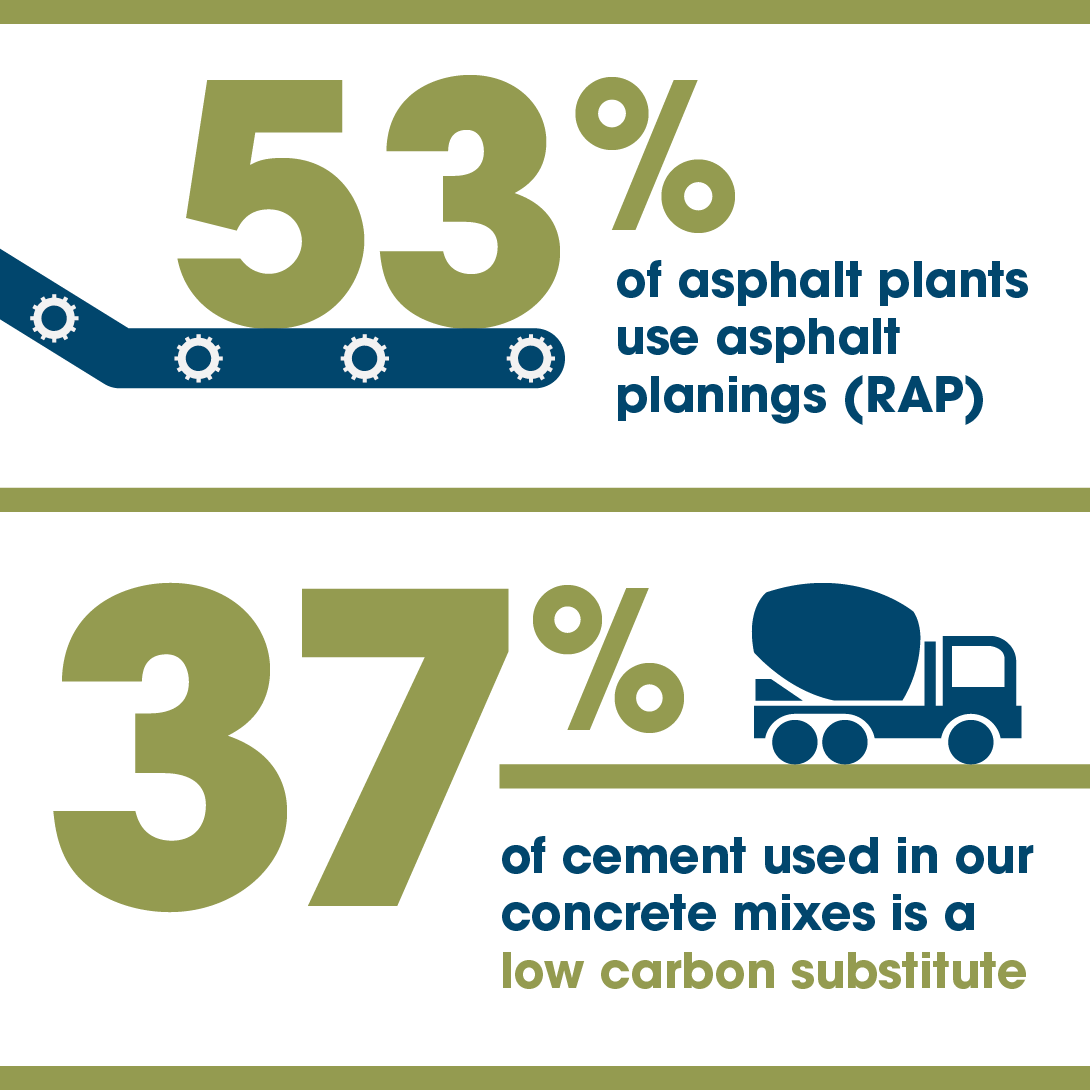
Ash shortage boosts Regen production
A shortage of fly ash from coal-fired power stations led to an upturn in Regen production in 2014. During the summer there was a severe dip in fly ash production due to electricity generation being switched from coal-fired power stations to biomass or gas. Read more
Nine-hour pump claims UK record
Product quality was a key factor in setting what is thought to be UK concrete pumping record on London’s Crossrail project. Read more