People
-
Our vision:
Zero harm in the workplace and a positive impact on communities around our sites. Effective partnerships and dialogue with stakeholders.
-
Strategy:
Ensure health and safety remains our number one priority; develop the skills of our workforce; make a positive contribution to the communities around our operations.
-
Action plan:
Focus on training, control of contractors and visitors, and hazard and risk assessments. Set targets to increase near hit reporting and introduce one-to-one safety conversations with all employees; introduce a formal induction process at every site; host and facilitate regular engagement meetings with stakeholders and communicate outcomes; reduce environmental incidents and emissions.
-
2020 targets:
Zero harm; five community events a year at every quarry; meet the targets set in the Mineral Products Association’s ‘Safer by Competence’ programme to 2017; reduce valid neighbour complaints year on year.
Health and safety
Fall in lost time injuries
The total number of lost time injuries (LTIs) fell from 32 to 31, but employee LTIs rose from 14 to 20. The employee LTI frequency rate of injuries per one million hours worked, which has been adopted as a standard industry indicator, also rose from 1.5 to the 2012 level of 2.1, based on the average number of people employed during the year.
We have helped the MPA to achieve its interim target to halve both the LTI frequency rate for direct employees and the cumulative number of contractor lost time injuries by 2014 based on 2009 figures.
The LTI severity rate for our own employees, derived from the total number of days lost, fell in 2014 from 62.4 to 49.3 – beating our previous lowest of 58.6 achieved in 2012.
A key part of improving our health and safety culture is to engage with our work force. In 2014 we re-launched our safety conversations programme and introduced one-to-one safety discussions for all employees.
We continued to invest in health surveillance to detect existing or underlying issues, and we again provided free check-ups – or health MoTs - for all employees. We also delivered comprehensive health and safety training for our staff, from both in-house specialists and external consultants through conference calls podcasts and on site events.
Number of lost time injuries
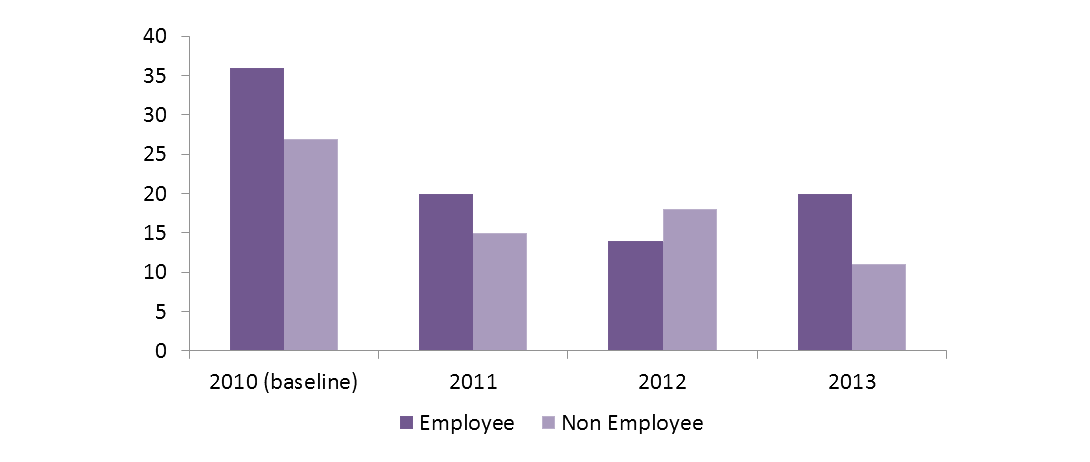
-
Lost time injuries data
Lost time injuries
2010 (baseline)
2012
2013
2014
Employees
36
20
14
20
Contractors
27
15
18
11
Employee severity rate
83.92
58.59
62.41
49.34
Employee frequency rate
3.23
2.08
1.52
2.05
Target: Zero harm
Stakeholder performance
Workshops improve communication
We continued our programme of stakeholder engagement workshops involving customers, trade associations, NGOs and community leaders and have gained some valuable feedback. Two sessions were held during the year featuring two-way dialogue and presentations from stakeholders. The second event included a visit to our Purfleet Regen plant.
Our employees remain an important stakeholder group and we continued to improve our internal communications through better use of the intranet platform, podcasts, employee forums and staff briefing meetings. CEO Patrick O’Shea carried out a series of 10 meetings across the country to explain the strategy, performance and prospects for the business.
-
Read more
The remit of our employee working groups has been extended from safety to embrace environmental, social and community affairs. At site level we have appointed sustainability reps to take responsibility for all these elements. They share best practice through regional cross-business line working groups, chaired by a divisional managing director, and representatives from the regional groups meet once a year with the executive board. Training of site-based reps is ongoing – all will have attended two individual training days in 2015 with a third day to follow next year.
Five of our sites are within national parks and we are active members of the Corporate Forum for National Parks, which encourages dialogue between the Campaign for National Parks, the park authorities and the businesses which operate within the parks.
Before submitting planning applications for new developments we consult widely with both statutory bodies and local residents. We held two public exhibitions during 2014 to present proposals for mineral extraction. The exhibitions provide an opportunity for local residents to view and comment on the proposals prior to planning applications being submitted. As members of the principal trade associations in our sector, we contribute to discussion and debate on a range of issues designed to improve our sustainability performance.
Target: To become a recognised leader in engaging with customers, suppliers, community leaders, NGOs and employees and developing collaborative projects to benefit sustainable development.
Environmental incidents and emissions
Complaints
As part of our management systems we record incidents (occurrences noted by our own staff which may or may not have led to a complaint) and complaints (arising from external sources).
Complaints increased in almost all business lines, although the total is still slightly below our target figure of 193 based on 2010. All complaints were acted on quickly and closed out to try and avoid recurrence. The number of self-reported incidents dropped.
We use our Entropy software to record incidents, near hits and complaints and improve reporting. It allows us to analyse complaints and introduce appropriate mitigation measures. Reports are generated monthly and systems are in place for recording and tracking required actions.
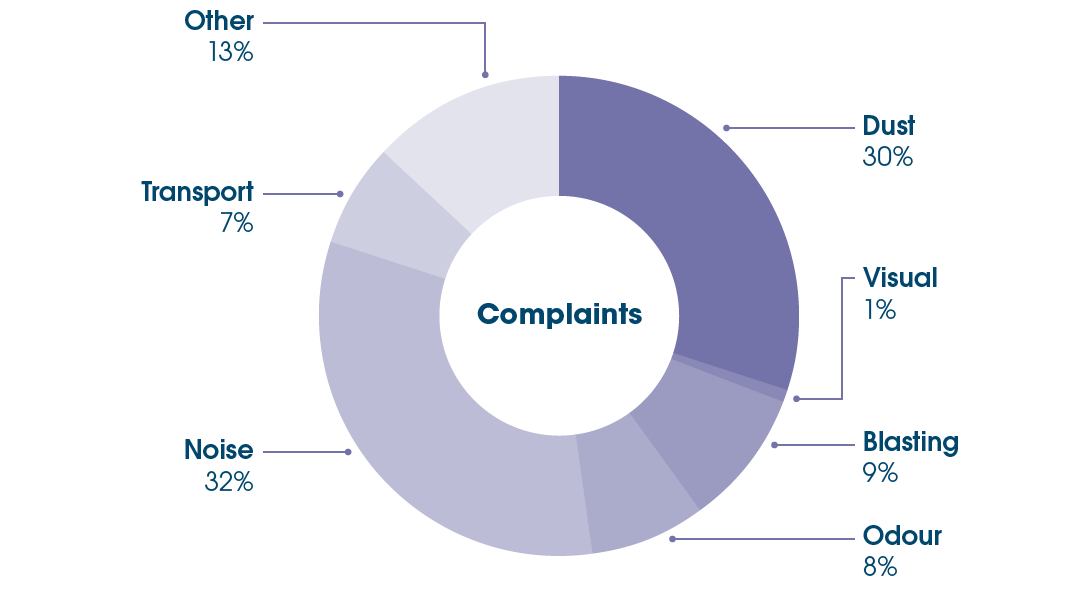
-
Incidents, complaints and prosecutions data
Incidents, complaints and prosecutions
2010 (baseline)
2012
2013
2014
Incidents
191
561
570
245
Complaints
294
263
132
185
Prosecutions
1
0
0
0
Target: 10 per cent year-on-year reduction in complaints based on 2010 figures.
Emissions from cement production
Emissions from the UK cement industry as a whole have reduced significantly over the last 15 years. Dust emissions have fallen from 0.33 to 0.10 kilogrammes per tonne of Portland cement (Pce). NOx emissions have halved from 3.34 to 1.63 kg/tonne PCe while SO2 emissions, which are related to the presence of volatile sulphur compounds found in the raw materials are down from 2.56 to 0.64 kg/tonne PCe. (Source: Mineral Products Association). These reductions have been achieved in the main through major investment in new plant and equipment.
All three of our cement plants operate at levels at or significantly below these industry averages and below EU best available technique (BAT) reference document levels. We continue to invest in new equipment to reduce emissions from our cement plants and publish annual reports on our website at www.hanson.co.uk.
Cement emissions to air
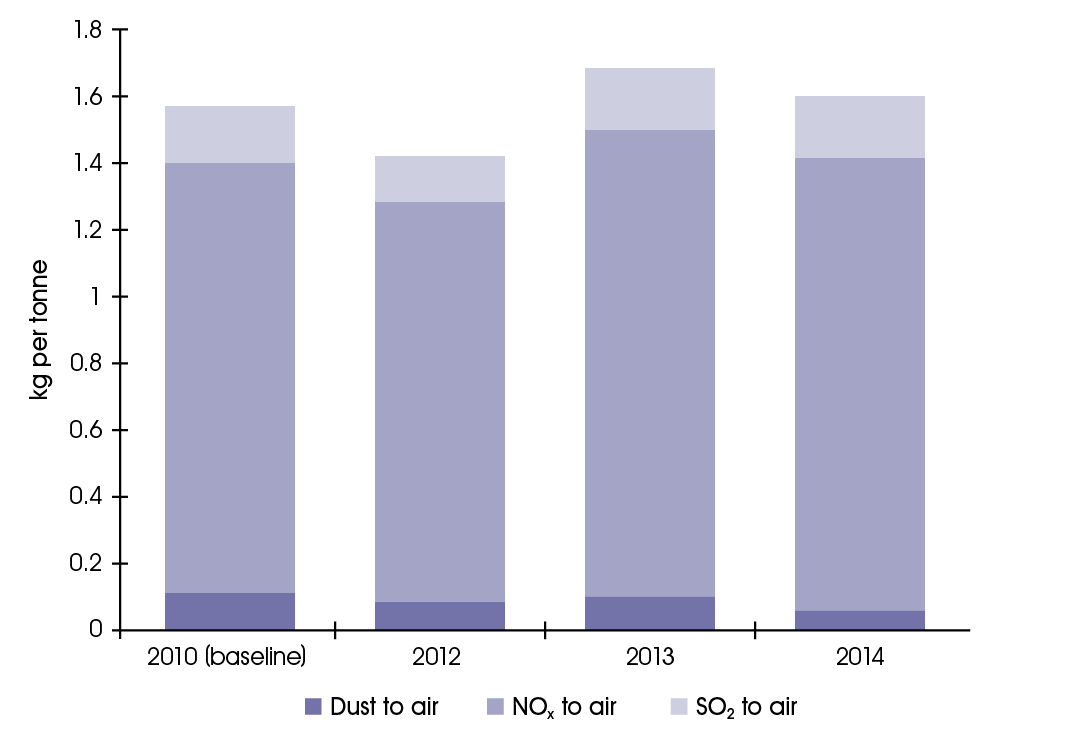
-
Cement specific emissions - kgs per tonne data
Cement specific emissions - kgs per tonne
2010 (baseline)
2012
2013
2014
Dust to air
0.11
0.08
0.10
0.06
NOx to air
1.29
1.20
1.40
1.36
SO2 to air
0.17
0.14
0.19
0.19
Targets: Reduce NOx emissions by 20 per cent and dust by 10 per cent by 2020 based on 2010 data and maintain 2010 SO2 level
Employment and skills
Spending on training increases
The number of staff employed at January 1, 2015 was 4,608. This fell to 3,480 with the divestment of our building products division in March 2015. Spending per head on training and skills rose during the year, with the focus on safety, health, environment and leadership. We continued with our talent management and succession planning programmes. A database called the Learning Management System (LMS) records and tracks training needs and provision and contains all employee training records.
We recognise that workplace diversity is a growing area of interest and importance. You can find a full breakdown of our employees by gender and age below.
We continue to provide a range of benefits to support employees. EmployeeCare provides a round-the-clock telephone counselling service through which employees can receive individual and confidential support on a broad range of work-related and personal issues, including financial management, stress, bereavement and relationships. Mysafeworkplace is a confidential service for employees to report anything from workplace harassment to fraud.
Employees by gender
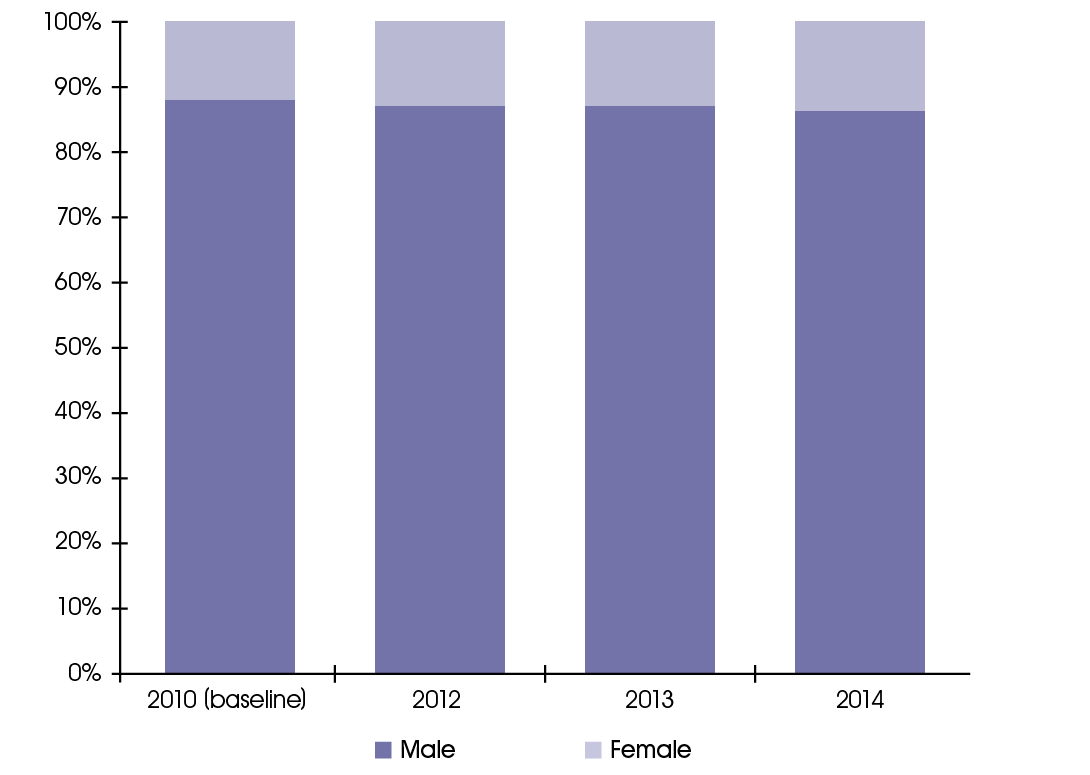
Employees by age
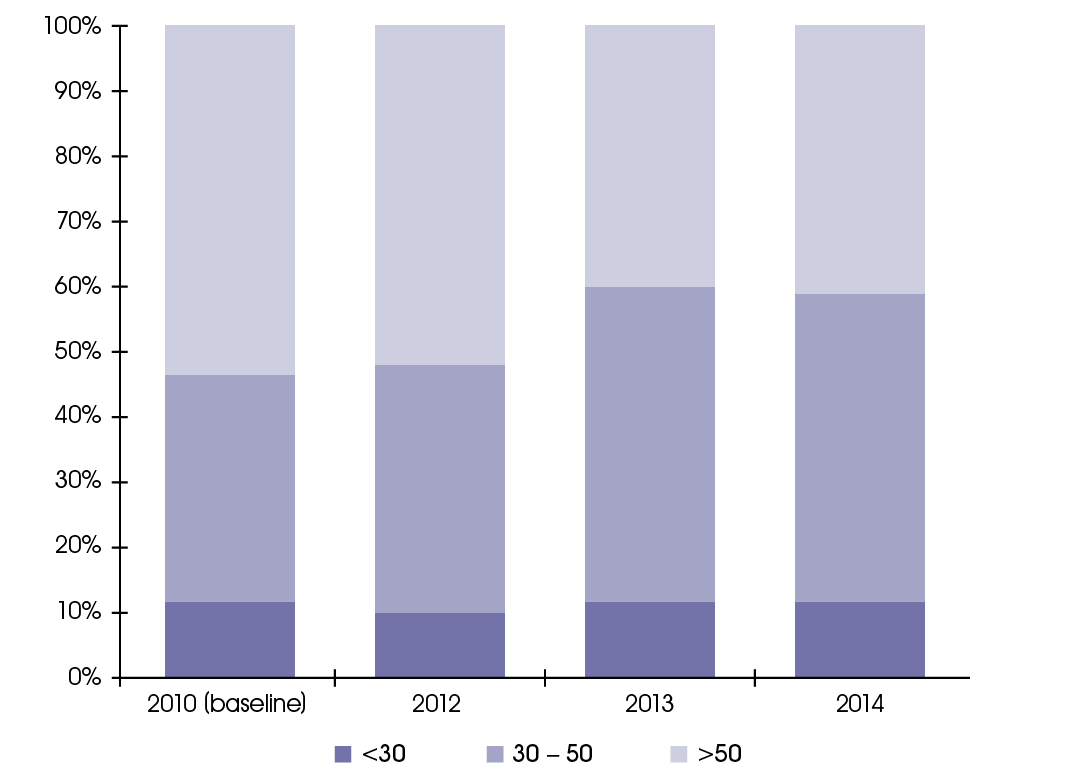
Local community
Site visits are encouraged
We recognise that our operations are part of the local community and we strive to be good neighbours. Many of our larger sites operate liaison committees attended by councillors, council officers and residents’ representatives. The number of sites with liaison activities was static at 41 but improved in real terms because we increased the number of events required from two to three.
Our three cement plants all produce community newsletters to keep residents and businesses informed about their activities and provide a conduit for further information.
We help charities and voluntary groups in communities close to our sites and offices through the Hanson in the Community scheme. In 2014 we provided cash or materials to support over 130 organisations to the value of £32,200.
Our employee charity matching scheme contributed £21,000 to 70 charities during 2014 and has helped raise more than £1.2 million pounds since its introduction in 1994. The scheme encourages employees to raise money for charity by matching their fund-raising up to £500.
We are corporate patrons of CRASH, the construction industry charity which provides accommodation for the homeless, and we support a number of other smaller environmental and community-based organisations and charities.
Sites with liaison activity (%)
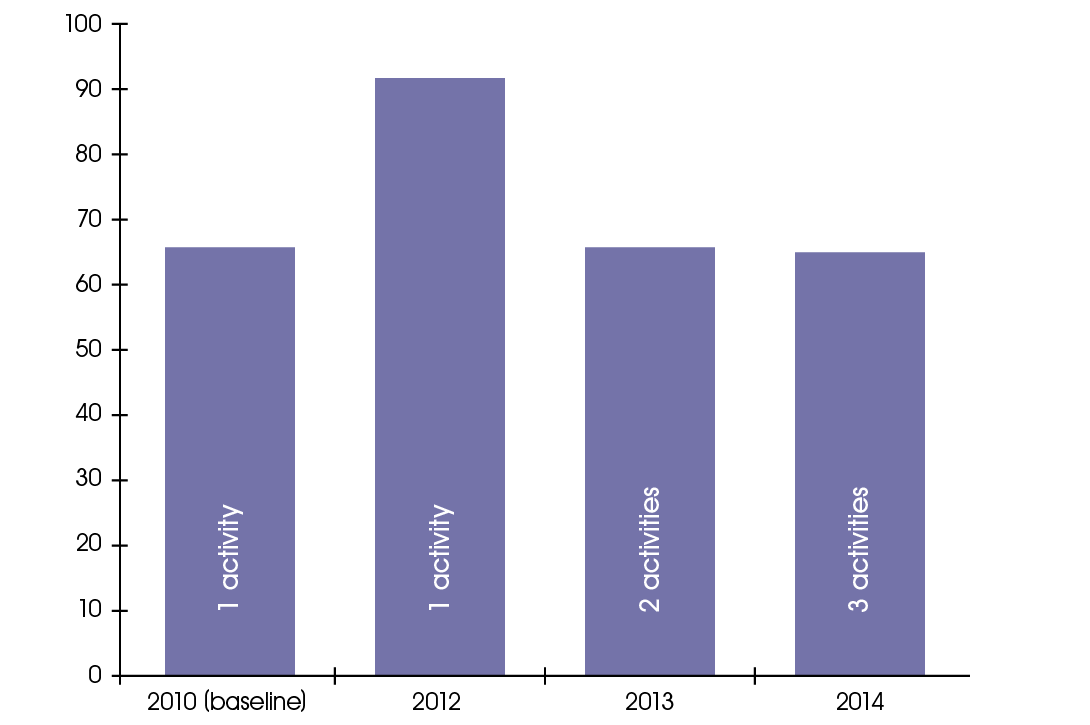
-
Community relations data
Community relations
2010 (baseline)
2012
2013
2014
Relevant sites
77
62
62
63
Sites with liaison activity
51
(1 activity)57
(1 activity)41
(2 activities)41
(3 activities)Sites with liaison activity
66%
92%
66%
65%
Visitor numbers
8,843
33,477
26,224
25,752
Target: At least five community liaison events a year at every quarry by 2020.
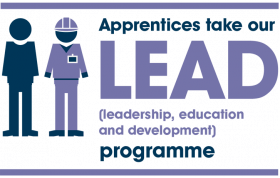
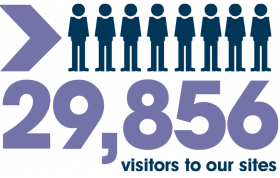
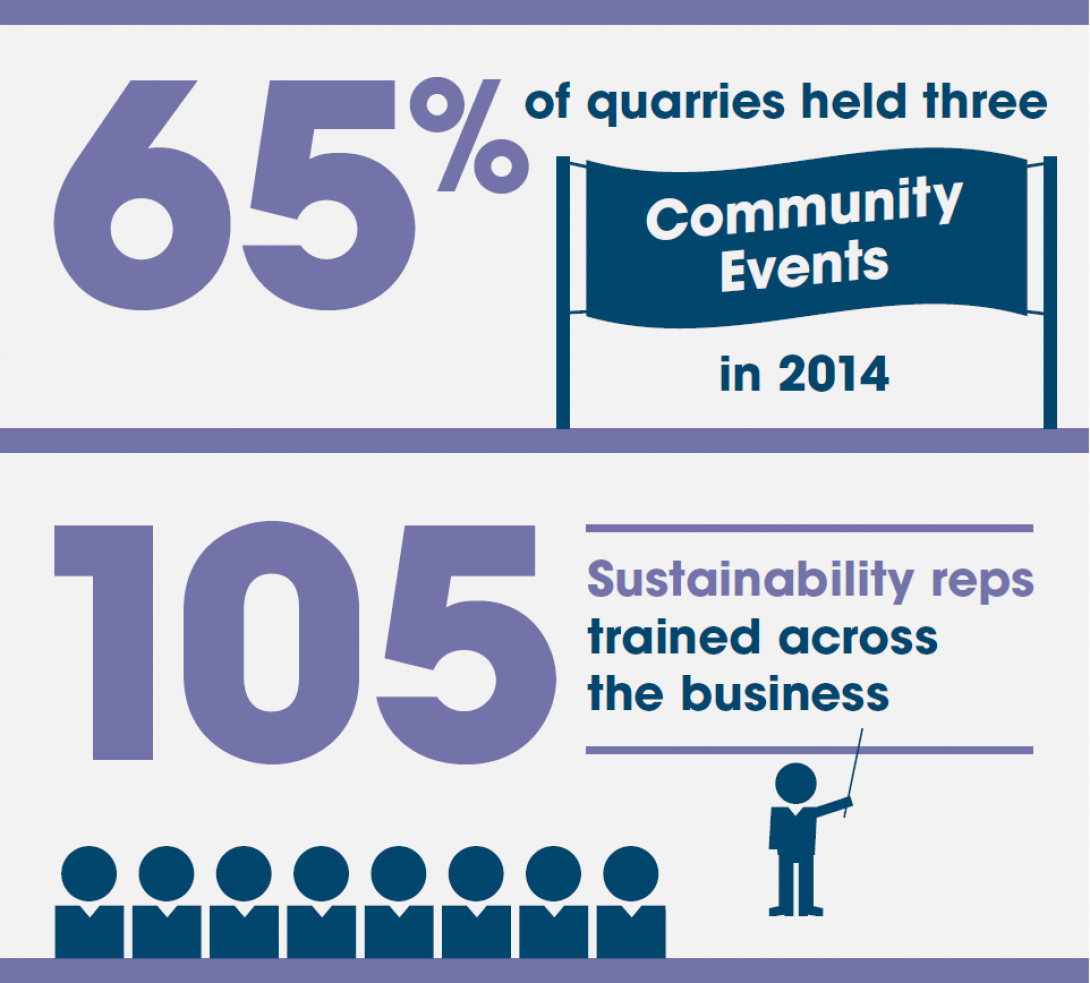
Safety week expands
Our annual health and safety awareness event was expanded from one week to three to reach more people face-to-face across the business. Read more
Former quarry site donated to community interest company
Hanson has donated 61 acres of land at a restored sand and gravel quarry at Hope in Flintshire to the Park in the Past community interest company to establish the world’s first reconstruction of a Roman landscape and eco-system. Read more
Phase two of industry-leading apprentice scheme launched
The latest group of recruits to join the Hanson Leadership, Education and Development (LEAD) higher apprentice programme started work in September 2014. Read more
Open days attract 1,400
More than 1,400 people attended open days at Ribblesdale and Padeswood cement plants. Read more